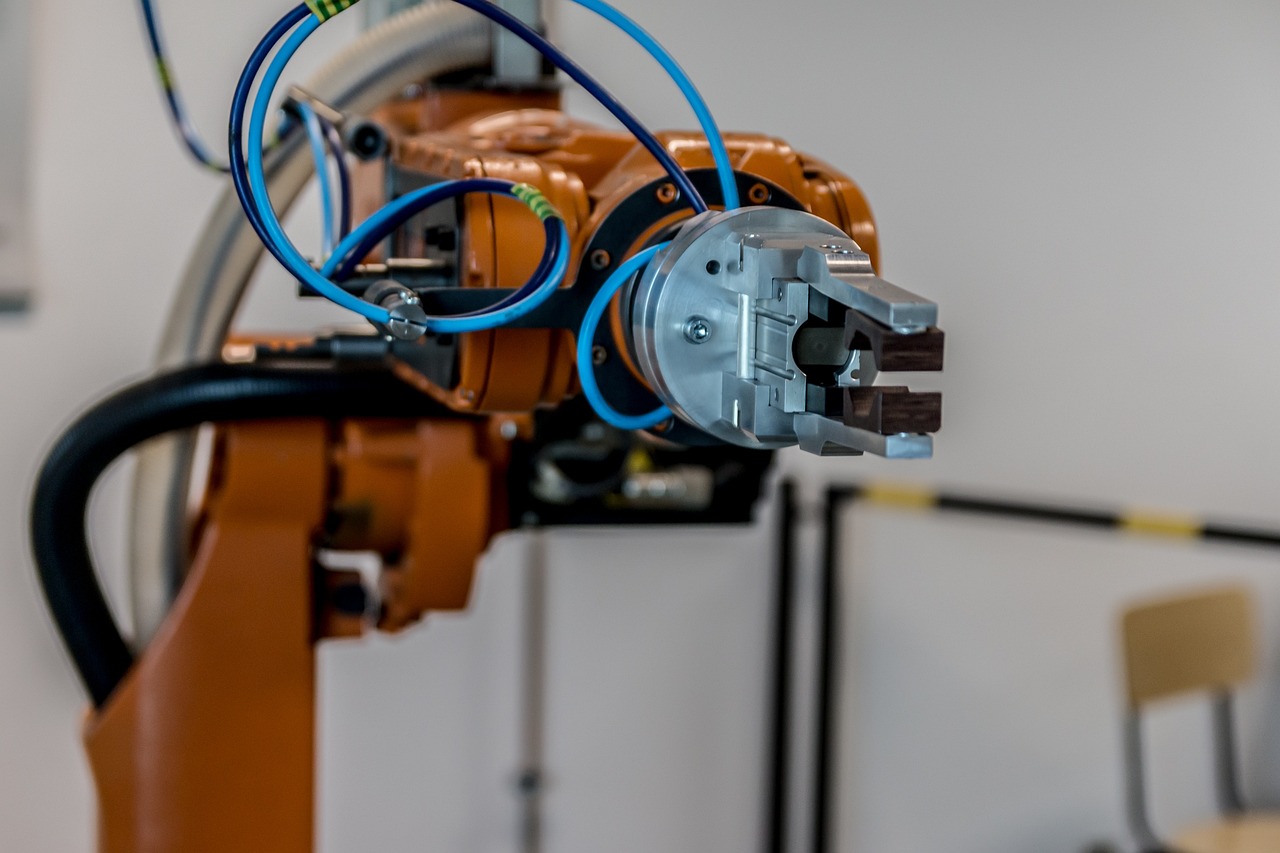
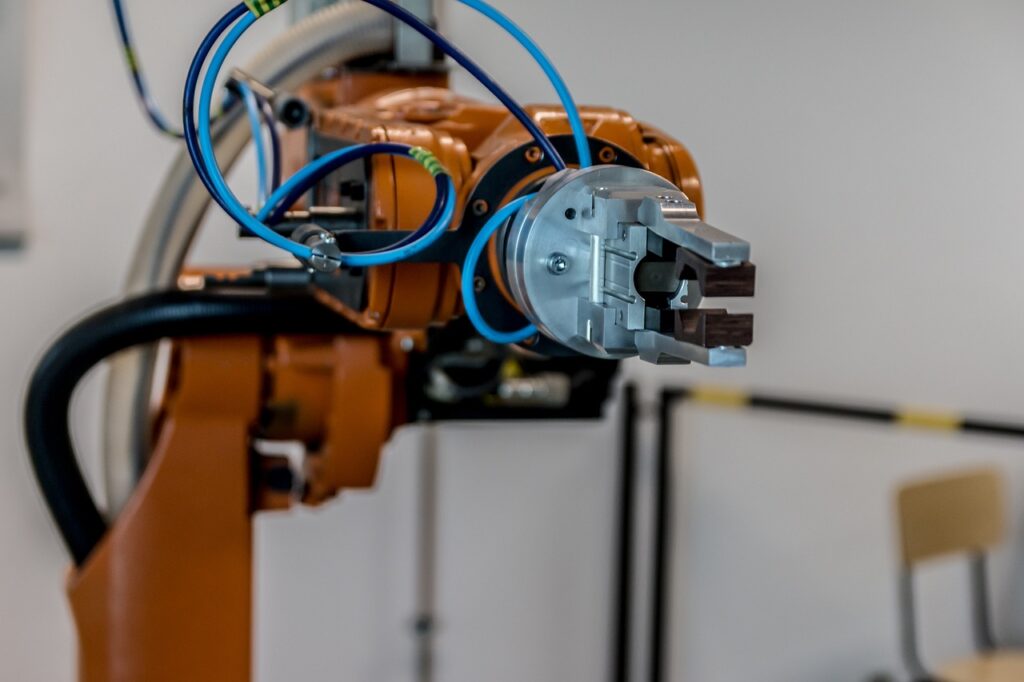
The top 10 applications of cobot arms showcase their incredible versatility, highlighting their role in reshaping the present and redefining the future of manufacturing. Get ready to explore a world where human ingenuity meets robotic prowess, unleashing the full potential of cobots in shaping the future of industry.
Advantages of Using Cobot Arms in Manufacturing
- Increased Productivity: Cobot arms operate tirelessly, leading to higher production rates and improved efficiency as they don’t experience fatigue or require breaks.
- Enhanced Safety: Designed to collaborate with humans, cobot arms incorporate advanced sensors to detect potential collisions or hazards. This eliminates the need for physical barriers, ensuring a safe working environment.
- Cost-Effectiveness: Compared to traditional industrial robots, cobot arms offer easy integration into existing workflows, requiring minimal setup time and reducing overall costs in terms of installation and programming.
- Flexibility: Cobot arms can be quickly programmed for various tasks on different product lines, enabling manufacturers to adapt rapidly to changing production demands.
- Small Footprint: With a smaller footprint, cobots are suitable for small-scale manufacturing operations where space may be limited.
- Precision and Repeatability: Cobot arms exhibit excellent precision and repeatability, particularly in tasks such as assembly or quality control inspections. This ensures consistent results and minimizes errors or defects.
- Ease of Use: User-friendly interfaces and intuitive programming options make cobot arms accessible even for non-technical personnel within a manufacturing facility, facilitating seamless implementation.
- Collaborative Opportunities: Cobot arms can interact collaboratively with human workers, enabling the execution of complex tasks that require both human dexterity and machine efficiency, such as welding or pick-and-place operations.
Top 9 Applications of Cobot Arms:
Top 1: Assembly and Production Lines
Assembly and production lines are important in manufacturing, requiring precision and efficiency. Cobots, or collaborative robotic arms, have revolutionized assembly tasks by being easily programmable for repetitive actions such as picking, placing, and connecting components.
With advanced sensors and safety features, cobots can work alongside human workers without risks. They seamlessly integrate into existing workflows, adapting to different product variations. Automating routine tasks with cobots reduces errors, ensuring consistent product quality.
This automation also frees up human workers’ time for more complex tasks, boosting productivity and job satisfaction. Cobots have become indispensable in various manufacturing sectors, collaborating with humans to enhance overall efficiency.
Top 2: Packaging and Palletizing
Cobot arms have brought about a revolutionary change in manufacturing by transforming packaging and palletizing processes. With advanced sensing capabilities, these robotic arms accurately identify and handle various packaging materials, ensuring consistent and error-free product packaging.
In palletizing, cobot arms excel at organizing finished goods on pallets, reducing manual effort and increasing efficiency. Their versatility allows them to adapt to different package sizes and weights, catering to changing production requirements.
Incorporating cobot arms in these operations leads to improved productivity, reduced labor costs, enhanced product quality, and overall operational streamlining, making them a transformative technology in manufacturing industries globally.
Top 3: Machine Tending
Cobot arms have transformed machine tending in manufacturing, automating tasks traditionally done manually. These robotic arms, equipped with sensors and cameras, enhance efficiency and precision in handling parts and materials for various machines. Notably, cobots can collaborate safely with human operators, eliminating the need for safety barriers.
They excel in tasks like loading raw materials, unloading finished products, tool changes, and quality checks across diverse applications such as CNC machining, injection molding, and more. Automation with cobot arms boosts productivity and maintains consistent quality, freeing human workers for more complex, important tasks.
Overall, cobot arm technology revolutionizes manufacturing with flexible automation solutions for machine tending.
Top 4: Quality Control and Inspection
Cobot arms are revolutionizing quality control and inspection processes in manufacturing. Equipped with sensors and cameras, these robotic arms provide precise and efficient product inspections, identifying defects with advanced vision systems.
They excel in repetitive tasks, ensuring accurate and consistent results over large product volumes. Collaborating seamlessly with human workers, cobot arms free up time for complex analysis, improving overall efficiency. With applications across industries, from electronics to automotive, cobots automate inspections, reducing errors caused by fatigue.
The integration of cobot arms brings benefits such as increased productivity, higher accuracy, and reduced costs, leading to improved customer satisfaction and making them an indispensable tool in the pursuit of manufacturing excellence.
Top 5: Material Handling
Cobot arms play an important role in revolutionizing material handling in manufacturing by offering efficiency and precision. These versatile robotic arms, equipped with advanced sensing and gripping capabilities, can handle a diverse range of materials, from small components to heavy loads.
Operating in tandem with human operators, cobot arms navigate tight spaces safely. In warehouses, they excel at sorting and organizing inventory, speeding up processes, and minimizing errors. Cobot arms are ideal for loading and unloading tasks, ensuring the careful handling of materials during production.
Their contribution extends to repetitive tasks like stacking boxes and moving heavy equipment, reducing strain on human workers while maintaining productivity. In essence, the integration of cobot arms transforms material handling in manufacturing, bringing agility, accuracy, and adaptability to the production cycle.
Top 6: Welding and Fabrication
Cobots have revolutionized welding and fabrication in manufacturing, offering precision and flexibility in working with various materials. They address challenges faced by human welders, such as repetitive strain injuries, by handling dangerous tasks with high heat levels, ensuring safety. Equipped with advanced vision systems, cobots accurately detect welding joints, providing precise adjustments for consistent quality control and reducing errors.
Their ability to reach tight spaces enhances efficiency in complex structures. The collaboration between humans and cobots allows operators to focus on important tasks while cobots handle repetitive or physically demanding jobs. Overall, the integration of cobot arms into welding and fabrication processes has significantly improved efficiency, safety, accuracy, and productivity in manufacturing industries globally.
Top 7: Painting and Coating
Cobot arms have revolutionized painting and coating processes in manufacturing, offering efficient and precise automation. Equipped with paint sprayers, cobots ensure consistent finishes, eliminating human errors and the need for rework. They can operate in hazardous environments, handling toxic chemicals without risking health and safety. The flexibility of cobots allows easy adaptation to different products or surfaces by programming desired patterns, colors, or materials.
Cobots increase productivity with longer operating hours and faster production rates, as they work tirelessly without fatigue. Cost savings result from minimal maintenance compared to traditional equipment and the absence of breaks or vacations. Beyond manufacturing, cobot arms find applications in automotive refinishing, aerospace engineering, furniture production, and art installations. With their precision, flexibility, and efficiency, cobot arms have become indispensable tools in various creative industries and manufacturing sectors.
Top 8: Pick and Place Tasks
Cobot arms are widely used in manufacturing for pick and place tasks, efficiently handling the precise movement of objects from one location to another. Programmed for precision and accuracy, cobot arms excel in handling diverse shapes, sizes, weights, and materials without causing damage. Equipped with advanced vision systems and sensors, they ensure accurate placement, reducing errors attributed to human fatigue.
Cobot arms can adjust their grip strength based on the object, ensuring a secure hold without harm. Automating pick and place tasks with cobots enhances productivity, reduces labor costs, and allows human workers to focus on more complex or creative roles. The benefits include increased efficiency, improved accuracy, and optimized human resource utilization in manufacturing processes.
Top 9: Collaborative Tasks with Humans
cobot arms are revolutionizing diverse industries, from assembly lines to collaborative tasks, enhancing efficiency and workplace safety. Their remarkable ability to collaborate with human workers on physically demanding tasks improves productivity and frees up time for complex responsibilities. Offering advantages over traditional robots, cobot arms are easy to program, adaptable, and fit into smaller spaces seamlessly.
The future holds promise with ongoing advancements in AI and machine learning, making these robotic assistants smarter and more autonomous. The rise of cobot arms signifies a new era in manufacturing automation, optimizing processes, and ensuring safer workplaces through collaboration with humans, driving innovation globally.