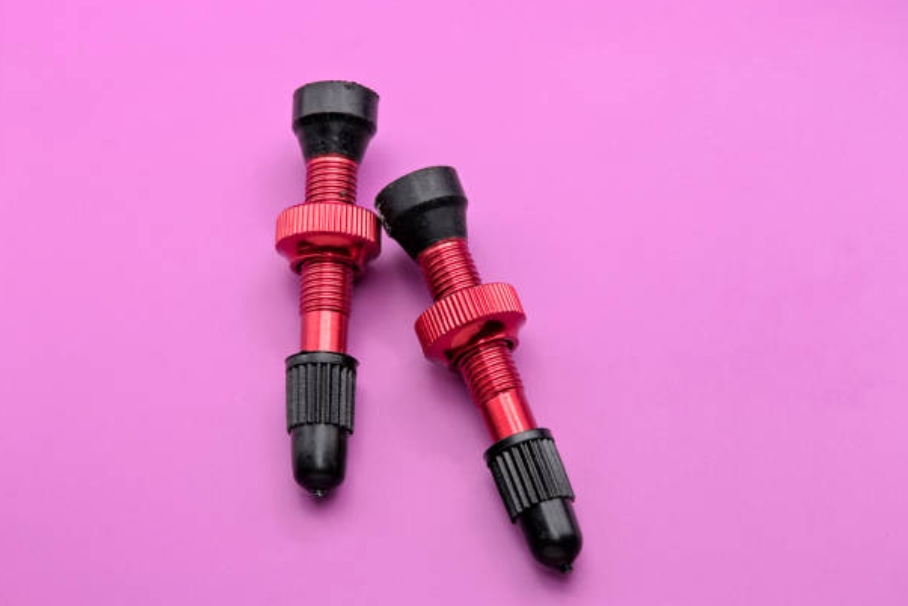
When it comes to enhancing the durability and aesthetic appeal of metal, anodizing is a popular choice. While many are familiar with anodized aluminum, the concept of anodized steel often sparks curiosity. This is because anodized steel is increasingly becoming a material of choice in various industries due to its enhanced properties.
Anodized steel offers a unique combination of increased corrosion resistance, enhanced wear properties, and striking visual finishes. Even so, it remains vital that you understand what anodized steel is and its benefits to guide you in determining if the material is the right choice for your projects. Keep reading this article to learn all you need to know about anodized steel.
What Is Anodized Steel?
two red sparkling anodized steel bicycle hubs
Anodized steel is a type of steel that has undergone an electrochemical process to enhance its surface properties. This method involves submerging the steel in an electrolytic solution and applying an electric current, resulting in a thick oxide layer forming on the surface. This oxide layer significantly improves the steel’s resistance to corrosion, wear, and other environmental factors, making it a durable and attractive material for various applications.
How the Anodizing Process Works
Unlike the anodizing of aluminum, which typically uses acidic solutions, steel anodizing often employs caustic solutions like sodium hydroxide (NaOH) or potassium hydroxide (KOH).
Here’s a detailed look at the process.
Preparing the Steel
The initial step in anodizing steel involves thorough surface cleaning. To ensure proper adhesion of the new oxide layer, you must remove any oils, dirt, or existing oxide layers. Start with degreasing the steel using a suitable solution to eliminate organic contaminants. Following this, rinse the steel with deionized water to remove any residual degreasing solution. For additional assurance of cleanliness, mechanical cleaning methods like sandblasting or abrasive brushing can be used to prepare the steel surface.
Caustic Solution Preparation
Once the steel is cleaned, the next step is to prepare a 50% solution of NaOH or KOH. This high-concentration caustic solution is essential for creating the desired oxide layer on the steel surface. Given the corrosive nature of these solutions, it’s crucial to follow proper handling and safety measures.
The Anodizing Process
After preparing the steel and the solution, submerge the cleaned steel in the caustic solution. Next, connect the steel to the positive terminal (anode) of a power supply while using a counter electrode made of steel, platinum, or nickel connected to the negative terminal (cathode). Ensure the solution is well-prepared and at the correct concentration.
Moving forward, initiate the electrolytic action by passing a current through the solution. This step forms a magnetite (Fe3O4) coating on the steel surface. Then, the current density must be controlled carefully to ensure uniform oxide layer formation. Maintain the solution at an optimal temperature, typically around 70°C, to facilitate the reaction. Keep in mind that using a magnetic stirrer helps keep the electrolyte solution evenly dispersed, preventing localized overheating and ensuring uniform coating.
Monitoring Parameters
The thickness of the anodic coating depends on several factors:
- Concentration of the Solution: Higher concentrations may lead to faster oxide layer formation but require more stringent safety measures.
- Voltage Applied: Higher voltages can produce thicker coatings but may also increase the risk of uneven coating or solution breakdown.
- Submersion Time: Longer submersion times result in thicker coatings, providing more robust protection against corrosion.
Post-Anodizing Treatment
After the anodizing process, it’s crucial to rinse the steel again with deionized water to remove any residual caustic solution. This step is essential to avoid further chemical reactions or damage to the newly formed oxide layer.
Benefits of Anodized Steel
Despite the challenges, some steel alloys can still benefit from anodizing, especially when specific conditions and treatments are applied. For those interested in DIY anodizing projects, using an anodizing kit can be a practical option. These kits provide all the necessary equipment and materials to anodize steel at home, allowing small-scale manufacturers to achieve professional-quality results without needing large-scale industrial equipment.
Here are the advantages of anodized steel:
Corrosion Resistance
The magnetite layer formed during anodizing provides excellent resistance to corrosion, protecting the underlying steel from rust and other environmental factors. This makes anodized steel suitable for harsh environments.
Durability
The anodized surface is harder and more resistant to wear and tear compared to untreated steel. This durability extends the lifespan of steel components.
Improved Wear Resistance
In addition to corrosion resistance, anodized steel also boasts improved wear resistance. The hard oxide layer protects the steel from scratches, abrasions, and other forms of physical damage. This makes it an ideal choice for high-traffic areas or components subject to frequent handling and wear.
Ease of Maintenance
Anodized steel surfaces are easy to clean and maintain. The protective oxide layer reduces the accumulation of dirt and grime, allowing for simple maintenance routines that preserve the material’s appearance and longevity.
Aesthetic Appeal
Anodized steel can exhibit a range of colors due to the thickness and structure of the oxide layer, enhancing the visual appeal of steel parts. This makes it suitable for decorative applications.
Drawbacks of Anodized Steel
Check the limitations of anodized steel below:
Process Complexity
The anodizing process for steel is more complex and requires careful control of several parameters, making it less straightforward than aluminum anodizing. This complexity can increase costs and require specialized equipment and expertise.
Surface Imperfections
Any surface imperfections on the steel before anodizing will be highlighted and possibly exacerbated after the process. This requires meticulous surface preparation.
Thickness Limitations
The thickness of the anodized layer is typically less than that achievable on aluminum, potentially limiting the level of protection in highly corrosive environments.
Environmental Concerns
The use of caustic solutions like NaOH and KOH raises environmental and safety concerns, requiring proper disposal and handling to mitigate environmental impact.
Applications of Anodized Steel
Anodized steel has become a material of choice in various industries. Check the pivotal applications of anodized steel below:
Automotive Industry
The automotive industry relies on anodized steel components for their resistance to harsh weather conditions as well as their durability. These parts include trim, handles, and other exterior features that require longevity and minimal maintenance.
Consumer Electronics
In consumer electronics, anodized steel is often used for its sleek appearance and scratch-resistant properties. This is particularly important for devices like smartphones, laptops, and other gadgets that are frequently handled.
Industrial Settings
In industrial settings, anodized steel is used for machinery parts, tools, and equipment that require robust protection against corrosion and wear. This prolongs the lifespan of the components and lowers maintenance expenses.
Can All the Steel Alloy be Anodized?
a pile of shiny faceted steel blocks
No, not all steel alloys can be anodized. The anodizing process primarily applies to aluminum and titanium alloys because their oxide layers provide significant benefits in terms of corrosion and wear resistance. However, anodizing steel, while possible, is less common and more complex due to the differences in their chemical properties.
Why Can’t All Steel Alloys Be Anodized?
Here are the major reasons all steel alloys cannot be anodized:
Chemical Composition
The primary reason not all steel alloys can be anodized lies in their chemical composition. Anodizing relies on creating a stable oxide layer on the metal’s surface. Aluminum and titanium form oxides that are both hard and protective. In contrast, the oxide layer formed on steel during anodizing can be less stable and more prone to spalling (flaking off), which limits its protective benefits.
Process Challenges
Anodizing steel requires more stringent control of the electrolytic solution and processing conditions. For example, the temperature and current density must be precisely controlled to prevent the steel from corroding rather than forming a protective oxide layer.
Surface Finish and Properties
The anodized layer on steel often results in a finish that may not be as aesthetically pleasing or as durable as that on aluminum or titanium. The oxide layer on steel can be more porous and less adhesive, making it less suitable for decorative applications where appearance is critical.
Tips for Anodizing Steel
anodized rose gold material coffee machine, kitchen appliance, on light background
Anodizing steel enhances its surface properties, providing better corrosion resistance, wear resistance, and aesthetic appeal. While more complex than anodizing aluminum or titanium, following certain guidelines can lead to successful results. However, if you find that anodizing is not the best option for your steel parts, exploring alternative coatings can provide similar benefits and meet your needs.
Here are some vital tips to consider when anodizing steel:
1. Choose the Right Alloy
Not all steel alloys are suitable for anodizing. It’s essential to select steel alloys known to respond well to the process, such as stainless steel or specific low-carbon steels. Each alloy has unique properties that influence its suitability for anodizing. Therefore, researching these properties is crucial. For instance, stainless steel contains chromium, which forms a passive layer that can be enhanced through anodizing. Selecting the appropriate alloy ensures that the anodizing process produces a stable, durable oxide layer, minimizing corrosion and spalling.
2. Surface Preparation is Key
Proper surface preparation by cleaning the steel thoroughly to remove any grease, oil, or contaminants remains vital for successful anodizing. You can use solvents, alkaline cleaners, or ultrasonic cleaning methods. Mechanical or chemical polishing can then create a smooth, uniform surface. This step ensures that the anodizing process results in an even and consistent oxide layer. A well-prepared surface allows the anodizing solution to penetrate uniformly, which is essential for achieving a high-quality finish.
3. Use the Right Anodizing Solution
The choice of anodizing solution can significantly impact the quality of the oxide layer. Consult with chemical suppliers or experts to select the optimal solution for your specific alloy and desired finish. You must also carefully control the concentration and temperature of the anodizing solution. These choices determine the thickness and properties of the oxide layer, impacting its durability and appearance.
4. Control the Process Parameters
Maintain precise control over the process parameters, including temperature, current density, and anodizing time. Steel requires different conditions compared to aluminum, so it’s important to monitor and adjust these variables closely. Consistency in these parameters will result in a more uniform and durable oxide layer. You can use automated systems to regulate these parameters and ensure repeatability.
5. Post-Anodizing Treatment
After anodizing, consider additional treatments to enhance the properties of the oxide layer. Sealing the anodized layer can improve its corrosion resistance. This can be done using hot water or specific sealing solutions, which help to close the pores in the oxide layer. Post-treatment processes, like dyeing or applying protective coatings, can greatly enhance the longevity of anodized steel. You can also use cold sealing methods, which involve immersing the anodized steel in a solution that reacts with the oxide layer to create a more impervious surface.
6. Test and Inspect Regularly
Regular testing and inspection are essential to ensure the quality of the anodized layer. You can use techniques such as microscopic examination, adhesion testing, and corrosion resistance testing to evaluate the effectiveness of the anodizing process. These tests help identify and correct any issues early on. Microscopic examination allows you to see the uniformity and thickness of the oxide layer, while adhesion testing ensures that the layer is well-bonded to the steel. These checks will help maintain high standards and consistent quality in your anodized products.
7. Consider Alternative Coatings
If anodizing proves to be too challenging or if the results are not satisfactory, consider alternative surface treatments. Options like powder coating, electroplating, or using protective films can offer similar benefits. These methods might be more straightforward and could provide the desired level of protection and aesthetics. These alternatives can be easier to apply and still achieve excellent results.
Conclusion
Anodizing steel significantly boosts the metal’s durability, corrosion resistance, and visual appeal, making it a highly valuable process in various industries. However, not all steel alloys are suitable for anodizing, highlighting the importance of selecting the right material and preparing it properly. By selecting the proper anodizing solution, controlling process parameters, and considering post-anodizing treatments, you can achieve high-quality results. Alternative coatings like powder coating and electroplating can be viable options for those encountering difficulties.
Are you ready to discover the unmatched benefits of anodized steel with Zintilon? Our expert anodizing services transform ordinary steel into durable, corrosion-resistant masterpieces, perfect for any application. Choose Zintilon for top-tier quality and exceptional performance. Contact us today to secure superior anodized steel solutions!