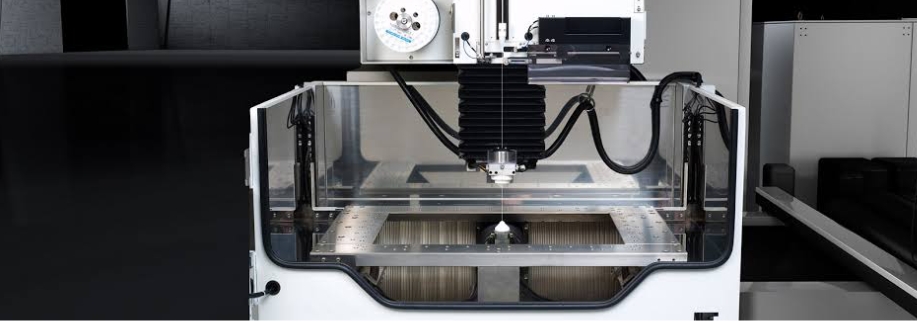
A close-up view of a wire cut EDM machine
Choosing the right Wire EDM machine is crucial for any precision manufacturing project. Wire EDM technology offers unique capabilities that can significantly enhance your production process. With so many machine options available in the market, it’s important to know what to look for to get the best performance and value for your needs.
This article will walk you through the essential factors to consider when selecting a Wire EDM machine. From understanding the basics to evaluating specifications and planning for future requirements, we’ll cover everything you need to make an informed decision. By the end of this article, you’ll have a clear understanding of what to look for in a Wire cutting EDM machine and be ready to choose the best one for your specific needs.
9 Key Factors to Consider When Choosing a Wire EDM Machine
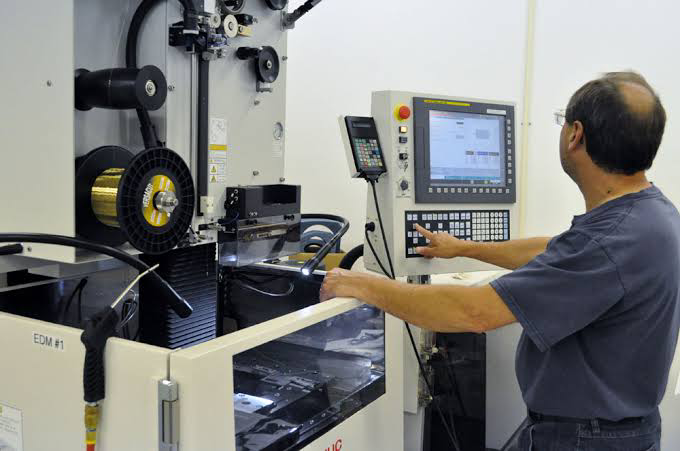
A machinist operating the wire EDM machine
Choosing the right Wire EDM machine involves evaluating several key factors to ensure it meets your specific needs and delivers optimal performance. Here’s what you should consider:
- Determine your specific needs
First, think about the materials you’ll be working with and their thicknesses. Are you cutting hard metals like steel and titanium or softer alloys? Knowing this helps you choose a machine that can handle your specific requirements. Consider the precision and tolerance levels you need. High-precision projects require machines with exceptional accuracy and repeatability. Also, evaluate the volume and frequency of your production. If you have high production demands, you’ll need a machine that can operate efficiently over long periods. By clearly defining your needs, you can narrow down your options and select a Wire EDM machine that aligns perfectly with your production goals.
- Speed and efficiency
Speed and efficiency are critical when selecting a Wire EDM machine. A faster cutting speed can significantly boost your productivity, but it’s essential that the machine maintains high precision at these speeds. Evaluate how efficiently the machine uses energy, as this can impact long-term operating costs. Look for features like automatic wire threading and real-time monitoring, which can minimize downtime and improve overall efficiency. By focusing on both speed and efficiency, you ensure that your Wire EDM machine can handle demanding production schedules while maintaining top-notch quality.
- Cost considerations
Cost is a major factor when choosing a Wire EDM machine. Start by evaluating the initial purchase price, but don’t stop there. You’ll also need to consider long-term operating costs, including power consumption, maintenance, and consumables like wire and dielectric fluid. Look into financing options that can make it easier to manage the upfront investment. Calculate the total cost of ownership (TCO) to get a comprehensive view of the financial impact over the machine’s lifespan. By thoroughly assessing both initial and ongoing costs, you can make a financially sound decision that balances budget and performance.
- Evaluate the power and electrical requirements
Understanding the power and electrical requirements of a Wire EDM machine is essential for smooth operation. Check the machine’s power consumption to ensure it fits within your facility’s electrical capacity. Efficient power usage can reduce long-term operational costs. Verify the electrical specifications for installation, including voltage and amperage, to avoid any compatibility issues. Ensuring your facility can support the machine’s electrical needs will prevent disruptions and maintain consistent performance.
- Machine specifications to consider
When choosing a Wire EDM machine, pay close attention to key specifications. Look at the cutting speed and efficiency; faster machines can boost productivity, but they must maintain precision. Check the machine’s accuracy and repeatability to ensure consistent, high-quality cuts. Also, consider the maximum workpiece size and weight capacity to ensure it can handle your projects. Verify the wire diameter compatibility, as different projects may require varying wire sizes. By evaluating these specifications, you can find a machine that enhances your production capabilities and fits your specific requirements.
- Control system and software capabilities
When choosing a Wire EDM machine, you’ll want to consider the control system and software capabilities. A user-friendly interface makes it easier to set up and operate the machine, reducing the learning curve and potential errors. Look for software that integrates well with your existing CAD/CAM systems, ensuring smooth transitions from design to production. Advanced features like real-time monitoring and diagnostics can help you track performance and quickly address any issues. By focusing on the control system and software, you ensure that your Wire EDM machine is easy to use and enhances your production efficiency.
- Maintenance and support
Maintenance and support are crucial factors when choosing a Wire EDM machine. You’ll want a machine that’s easy to maintain to minimize downtime and extend its lifespan. Look for models with accessible components that simplify routine maintenance tasks like cleaning and replacing parts. Additionally, consider the availability of replacement parts and the manufacturer’s support services. Good technical support and readily available parts can make a significant difference in resolving issues quickly and efficiently. By prioritizing maintenance and support, you ensure your Wire EDM machine remains reliable and operational for years to come.
- Brand reputation and reviews
When selecting a Wire EDM machine, the brand’s reputation and customer reviews are critical. Look for manufacturers known for producing reliable, high-quality machines. Read online reviews and testimonials to understand other users’ experiences. Trustworthy brands often offer better support and more durable machines, ensuring your investment is well-protected. Industry awards and recommendations can also guide you towards reputable manufacturers. By focusing on brands with strong reputations and positive feedback, you can make a more informed decision and invest in a machine that will meet your expectations.
- Future-proofing your investment
When choosing a Wire EDM machine, think about how it will fit into your long-term plans. Look for machines that offer scalability and upgradability, allowing you to enhance capabilities as your business grows. Ensure the machine can adapt to future technological advancements, such as software updates and new cutting techniques. This flexibility ensures your investment remains relevant and efficient over time, providing long-term value and reducing the need for frequent replacements. By future-proofing your investment, you ensure that your Wire EDM machine continues to meet evolving manufacturing needs.
Conclusion
Choosing the right Wire EDM machine is essential for enhancing your manufacturing capabilities and achieving high precision. By considering your specific needs, evaluating key machine specifications, and thinking about future scalability, you can ensure your investment is well-suited to your production goals. A well-chosen Wire EDM machine will boost productivity, maintain quality, and provide long-term value, supporting your business’s growth and success. Ready to find the perfect Wire EDM machine? Contact Zintilon today for expert advice. They also offer top-notch wire EDM cutting services.
FAQs
1. What should you consider when choosing a Wire EDM machine?
When choosing a Wire EDM machine, you’ll want to consider factors such as cutting speed and efficiency, accuracy and repeatability, and the machine’s maximum workpiece size and weight capacity. Also, check the wire diameter compatibility. Don’t forget to evaluate the control system and software capabilities, maintenance and support options, and the overall cost, including both initial purchase price and long-term operating expenses.
2. How does Wire EDM work, and what are its applications?
Wire EDM (Electrical Discharge Machining) uses a thin, electrically charged wire to cut through metal by creating sparks that erode the material. This non-contact process is perfect for producing intricate shapes and fine details without deforming the workpiece. You’ll find Wire EDM commonly used in industries like aerospace, automotive, medical device manufacturing, and mold-making, where high precision and the ability to cut hard materials like steel and titanium are essential.
3. Why is brand reputation important when selecting a Wire EDM machine?
Brand reputation is crucial because it reflects the reliability and quality of the machines produced. Choosing a machine from a reputable brand ensures you get a durable, high-performance machine with better customer support and readily available replacement parts. Reading customer reviews and industry recommendations helps you make an informed decision, ensuring a better return on your investment.